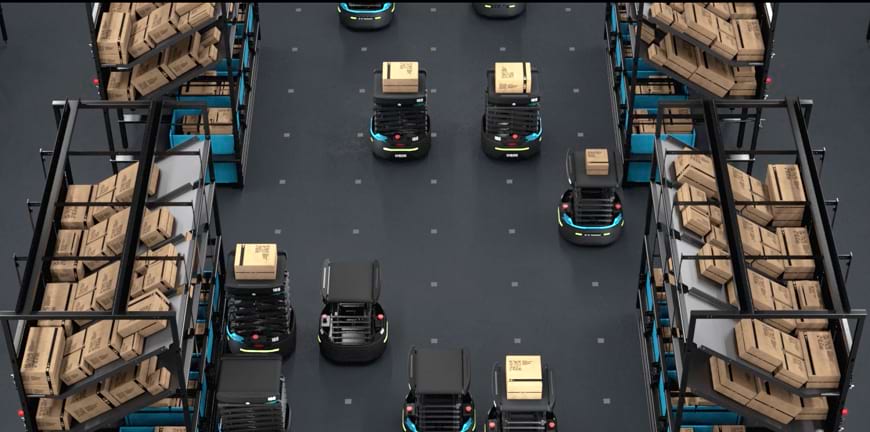
What are sorting robots?
Sorting robots are a type of stationary or mobile robots that enable fast and efficient sorting of goods/parcels based on end destination, categorisation and more. These robots use a combination of sensors, cameras, actuators, and other mechanical components to detect, characterize, and sort objects into the correct bin. Their sorting process is tailored to meet the specific needs and requirements of each business and is adapted to the type of objects/parcels being sorted.
Sorting robots have become increasingly important in recent years due to the benefits they offer over manual and conventional sorting methods, including higher efficiency, accuracy, and speed. They are used across various industries, including e-commerce, logistics, manufacturing, agriculture, and recycling.
Use of sorting robots in different industries
Sorting robots have various applications across different industries, including:
- Manufacturing: We often see the need for these robots in kitting for assembly lines, spare order consolidation, quality checks and rejection handling, etc. They can sort items rapidly with minimal errors, which enhances the overall productivity and efficiency of the manufacturing process.
- Logistics & Warehousing: Within the supply chain and warehousing industry, sorting robots are involved largely with sorting parcels or bulk units as per customer or store orders, delivery mode and 3 PLs, mid-mile or last mile destinations, returns sorting, etc. They can sort a vast volume of packages and parcels accurately, ensuring timely delivery to the designated location.
- Food processing: Sorting robots are primarily used in the food processing and packaging industry to sort fruits, vegetables, nuts, and other food items based on quality, size, shape, and defects. By detecting and removing defective or contaminated items, they help ensure food safety and reduce waste.
- Recycling: They are deployed in recycling facilities to sort different materials, such as plastic, metal, and paper, based on their properties. They can efficiently and accurately sort materials for recycling, thereby reducing the environmental impact of waste disposal.
Img. Sorting system used in recycling plants (Ref. Research gate)
- Retail: Sorting robots have become more prevalent in the retail industry to streamline the consolidation and organization of orders based on store locations and inventory replenishment needs. These robots aid in the prompt delivery of necessary items to retail stores.
- Pharmaceutical: In the pharmaceutical industry, they are used to sort and package medications based on their dosage and packaging requirements. They can handle small, delicate items with high accuracy and speed, reducing the risk of errors in the sorting process. Expired medicines from retail stores need to be sorted based on different sources before getting disposed of and sorting robots are capable of performing this function.
What are the sorting process challenges in the express logistics industry?
The sorting process in the express logistics industry can present several challenges, such as:
Handling a high volume of packages: Express logistics companies often have to process and sort a vast number of packages every day, which can be a daunting task. Sorting them manually can lead to a loss of accuracy and thus can increase the number of missorts and order returns.
- Warehouse Space: In order to promise faster delivery times, warehouses are moving closer to urban clusters. With the concept of dark stores, logistics players are promising deliveries within the hour and need to be positioned within the most premium localities in metro cities. The rising expenses of real estate and the large area required for setting up manual/traditional automation methods of package sorting can pose a serious bottleneck in meeting the modern-day expectations and needs of eCommerce.
- Manual Labour: Sorting a high volume of packages requires recruiting personnel on a large scale. As demand is increasing rapidly, facilities are getting larger, and relying solely on human resources can lead to higher fatigue, downtime and breach of delivery deadlines. In addition, the involvement of human resources increases the likelihood of missorts, which can further affect delivery timelines and customer experience.
- Meeting delivery deadlines: Express logistics companies take pride in their ability to deliver goods swiftly. Sorting packages promptly and accurately is critical to meeting delivery deadlines. With manual processing and multi-tiered sorting, it takes longer time and more touch-points to sort parcels. This leads to suboptimal delivery SLAs.
- Managing varying package sizes and shapes: Packages come in different sizes and shapes, which can make sorting a challenging task. Without the flexibility and customizability of sorting systems and robots, logistics players will be limited in their capability to handle diverse orders efficiently.
- Handling fragile and delicate items: Some items may require special handling due to their fragility or sensitivity. Sorting these packages requires care and attention to prevent damage. Manual handling at high speed and longer distances comes with its own downsides like damages to the label, packaging and the parcel itself.
Legacy systems used in automating the sorting process
Automated sorting systems have been around for many years, and several legacy systems have been used to automate the sorting process. Some of these legacy systems include:
- Conveyor belt systems: They are one of the oldest and most common sorting systems that are used in a wide range of industries, such as manufacturing, logistics, transportation, and mining. The most commonly used conveyor belt systems for the sorting process are Crossbelt Sorter, Tilt Tray Sorter, Bombay Sorter, Sliding Shoe Sorter etc. Each of these systems is designed to handle different parcel sizes, weights, throughput and no. of destinations. New variations in this technology involve sorting modules like Articulated Roller Belt, Ball Belt, Swivel Wheel and Omni-wheel for diverting parcels from the main conveyor lines to chutes.
- Put to Light: Put-to-Light (PTL) sorting technology is utilized in warehouses and distribution centres to fulfil orders efficiently. This system involves placing items to be picked in separate bins or totes, with each bin having a unique identifier or barcode. The bins are then arranged on shelves or racks in a grid pattern. When an order is received, the system instructs a picker to the first item’s location, and the picker scans the bin’s barcode. The PTL system lights up a display over the bin, indicating the quantity of the item to be picked. The picker selects the necessary amount of the item and places it in the bin. Once all the items have been picked, the system directs the picker to the packing station for packaging and shipment preparation.
Img. Graphical representation of Conveyor belt sorter used with Articulated Arm
Types of sorting robots
There are several different types of sorting robots, each with its unique features and capabilities. Some of the key types and their use in various industries are mentioned below.
XY Gantry Robots: XY gantry is a type of robotic system used in various industries for precision movement and positioning of objects. A gantry is a structure that consists of two or more legs that support a bridge-like structure. In the case of an XY gantry, the bridge is typically a horizontal beam that moves along the X and Y axes using linear motors or ball screws.
The gantry is often used in applications where a large workspace is needed, such as in the construction industry or for large-scale manufacturing. The end effector used in the case of a gantry robot is a tilt tray, which drops parcels/packages at predetermined destinations.
However, with this type of sorting robot, the maximum throughput that can be achieved is approximately 600 packages per hour, with a maximum of approximately 60 destinations. Hence, a presort of the packages is needed which increases the cost to deploy them.
Articulated Arm: A robot manipulator, commonly known as a robotic arm, is a programmable machine that emulates the functions of a human arm. Its links are interconnected by joints that facilitate either rotational motion (typical of articulated robots) or linear displacement (translation). The manipulator’s links form a kinematic chain, with the end effector representing the business end of this chain, much like a human hand. The end effector’s design can be customized to perform various tasks, including but not limited to welding, gripping, and sorting.
An articulated arm can sort parcels with a throughput of approximately 600 packages per hour but due to the mobility of the robot being an issue, the maximum destinations that it can sort into is ~60. Hence, in this case, as well, a presort of the packages is needed increasing the deployment cost.
Mobile Robots: They typically consist of a conveyor belt or tilt tray mounted on top of a mobile robot as end effectors. Using various sensors and devices, the robot detects the attributes of each item, such as its size, weight, shape, colour, or barcode, and determines the appropriate destination for each item based on the sorting criteria. The robot moves along the designated area and puts the parcel in the appropriate bin. These sorting robots are currently the most advanced technology in their field and are enabling customers to enhance their sorting efficiencies while also minimizing their warehouse space requirements. Mobile robots can be further classified as the following.
- Elevated Mobile Robots: They are robots designed for automated material handling and sorting tasks in warehouses and distribution centres. These robots typically operate on an elevated platform or track system that allows them to move above and around other machinery and obstacles in the warehouse. The robots use advanced sensors and computer vision technology to identify and sort items based on their size, shape, weight, and other characteristics.
Image credits: Robotics 247 article (Geek+ and FDL Group Implement Sorting Robots to Accelerate E-Commerce)
Elevated mobile robots can handle a wide range of products and offer several benefits over traditional sorting methods, including increased efficiency, accuracy, and speed. They can work around the clock without fatigue, reducing the need for human labour and minimizing the risk of errors and accidents.
- Mezzanine Platform-based Mobile Robots: These are autonomous robots utilized in warehouses and distribution centres to sort and transport items. They incorporate a mezzanine platform — an elevated structure above ground level — to move goods from one place to another. By utilizing the mezzanine platform, these robots can move both horizontally and vertically within the warehouse, thereby increasing storage efficiency. Equipped with sensors and cameras, they can navigate through the facility and avoid obstacles. Barcode scanning or other identification methods are used to sort items, after which the robots transport them to their designated location. The robots use either a conveyor belt or a tilt tray as the end effector to sort packages or parcels to their assigned locations.
This type of system is especially useful for e-commerce fulfilment centres that require high-speed sorting and transportation of a large volume of items. Overall, mezzanine platform-based sorting mobile robots are a highly efficient solution for warehouse automation, reducing labour costs, enhancing productivity, and optimizing space utilization.
- Direct Sorting Mobile Robots: These are autonomous robots designed to sort items in warehouses or manufacturing facilities. They use a combination of sensors, algorithms, and artificial intelligence to navigate through the facility, identify items that require sorting, and place them in their respective locations. Typically, direct sorting mobile robots employ a set of predetermined rules or algorithms to sort items, based on their type, size, shape, weight, or other characteristics. The robot scans the item, compares it to the rules, and determines where it should go.
Unbox robotics mobile robots parcel sortation system “UnboxSort”
The main advantage of direct sorting mobile robots is their flexibility, as they can be programmed to sort a wide range of items and can be easily reprogrammed to accommodate changing sorting needs. Furthermore, they are autonomous and can operate continuously without breaks or rest.
Type of Sorting Robot | Throughput (Packages per hour) | Destinations |
---|---|---|
XY Gantry | 600 pph | ~60 Destinations |
Articulated Arm | ~600 pph | ~60 Destinations |
Mobile Robots | 500-20000 pph | ~50-1000 destinations |
Table describing throughput capacity and sorting destinations achievable in different types of sorting robots
What are the advantages of sorting robots?
In today’s fast-paced world, sorting robots have become a popular choice for many businesses. They come with several advantages that make them an excellent choice for businesses looking to streamline their operations.
1. Increased Efficiency and Productivity
Sorting robots are designed to sort items significantly faster than humans. Sorting goods at a speed that human employees cannot achieve is possible with a sorting robot. This means you can perform jobs more quickly, resulting in enhanced efficiency and production. By deploying sorting robots, you significantly reduce the amount of time required to sort goods and focus on other important functions.
2. Improved Accuracy
One of the most significant advantages of sorting robots is their ability to sort items accurately. Sorting robots use advanced algorithms and sensors to identify and sort items based on their shape, size, and weight. This means that sorting robots can identify and sort items that may be difficult for humans to differentiate. With improved accuracy, businesses can reduce the number of errors and ensure that the right products are shipped to the right customers, thus reducing the cost of return processing.
3. Cost-Effective
Sorting robots can operate 24/7 without the need for breaks, unlike human workers who require regular breaks and time off. This means that sorting robots can work for more extended periods, which translates into reduced labour costs. Additionally, sorting robots can work in hazardous environments, eliminating the need to purchase expensive safety equipment for human workers. While the initial cost of purchasing sorting robots may seem high, they will be cost-effective in the long run. With the availability of the Robots-as-a-Service (RaaS) model, a company can easily deploy sorting robots without incurring upfront capital expenditures.
4. Improved Working Conditions
Sorting robots can work in hazardous environments, such as those with toxic fumes or extreme temperatures, without putting human workers at risk. By deploying sorting robots, businesses can improve working conditions for their employees and reduce the risk of workplace accidents. This can lead to improved employee morale, which translates into increased productivity.
5. Scalability
Sorting robots can be easily integrated into warehouses and existing production lines, making them an excellent choice for businesses looking to scale up their operations. As the demand for products increases, businesses can deploy more sorting robots to increase throughput without the need for additional human workers. This means that businesses can scale up their operations quickly and efficiently, without incurring significant labor costs.
6. Customization
These robots can be programmed to sort objects based on specific criteria, allowing businesses to customize the sorting process to meet their unique needs. One example of a unique application is using sorting robots to process returns by using sensors and cameras to identify and classify returned items from customers. The robots can then sort the items based on their type, size, and condition, and direct them to the appropriate storage or processing area. This process is faster and more accurate than manual sorting and can help reduce the time and labour required for returns processing.
Applications of sorting robots across the express logistics supply chain
The increasing demand for efficiency, accuracy, and speed in the flourishing express logistics supply chain industry has led to the increased adoption of sorting robots in recent years. Here are some of their key applications based on different legs of this industry.
1. Fulfilment Centers (First mile): A fulfilment centre serves as the hub of the supply chain, overseeing all logistics processes required to move goods from sellers to customers. Its responsibilities include managing the entire order fulfilment process, such as order picking, processing, packaging, and shipping. Through the assistance of a third-party logistics (3PL) provider, eCommerce retailers can leverage the centre’s services to receive, process, and fulfil customer orders, resulting in streamlined operations. The ultimate goal of the fulfilment centre is to ensure prompt delivery of online orders to mid-mile distribution centres for further sorting and dispatch to customers.
When a customer places an order, the products are usually kept in a warehouse or a distribution centre. To consolidate these products according to the customer’s order, automation systems like sorting robots, conveyor sorters, articulated arms, etc. are employed. This implies that the systems will recognize the particular products needed for the order and bring them together in one location for further processing.
Subsequently, the consolidated products are sent for packaging. At this stage, the sorting robots play a crucial role once again by sorting the packages based on their destination, which is typically the nearest distribution centre to the customer’s location. By using sorting robots, the packages can be efficiently and precisely sorted, reducing the likelihood of errors or delays.
2. Distribution Centers (Mid mile): A distribution centre is a type of warehouse that is designed to receive, store, and distribute finished goods to other locations or directly to end customers. These facilities are strategically located to ensure that goods can be transported to their final destination as quickly and efficiently as possible.
The primary function of a distribution centre is to manage inventory and fulfil customer orders. To achieve this, the facility is typically equipped with a variety of storage systems, such as pallet racks, shelving, and bins, to store goods in an organized and accessible manner. The distribution centre may also use advanced inventory management systems, such as RFID or barcode scanning, to track inventory levels and monitor stock movements.
At the distribution centre, sorting systems are deployed to categorize packages or items based on their intended destinations. These packages are then sorted using either traditional sorting systems or mobile sorting robots and subsequently transferred to the final stage of the express logistics supply chain, which is commonly referred to as the “last mile.”
Distribution centres also offer value-added services such as kitting, assembly, labelling, and quality control. These services allow companies to customize their products to meet customer needs and improve the overall quality of the goods. Overall, these centres are critical components of the supply chain that enable companies to efficiently manage inventory, fulfil customer orders, and add value to their products.
3. Last Mile (Last-mile delivery): Also known as last-mile delivery, refers to the transportation of goods from a retail store or transportation hub to the final delivery destination. It encompasses various delivery options, such as same-day, next-day, express, or standard delivery, and is the last stage in the delivery process.
The primary objective of last-mile delivery is to ensure speedy delivery, which translates to customer satisfaction. However, the challenge of cost-effectiveness arises because the last mile is often the most expensive part of the delivery process. The industry needs to adapt by exploring technological advancements to address this challenge. Sorting systems are used in these centres to ensure that the packages are sorted as per the zip code or the delivery van route and dispatched for delivery. With the use of sorting systems, last-mile delivery becomes cost-effective and is driving the growth of a technology-first e-commerce delivery partner market.
4. Return centres: Within the express logistics industry, return centres typically work by providing a centralized location for customers to return products or packages that they have received but no longer want or need. These centres are often managed by the logistics company itself or by third-party providers that specialize in processing returns.
When a customer wants to return a product, they can typically initiate the process through the logistics company’s website or by contacting customer service. The logistics company then generates a return shipping label and provides instructions for the customer to package the item and drop it off at a designated return centre or arrange for pick-up.
At the return centre, the returned products are typically inspected to ensure they are in good condition and can be resold or returned to the manufacturer. Depending on the type of product and the reason for the return, it may be sent back to the retailer, or the manufacturer, or even disposed of if it cannot be resold.
The logistics industry relies heavily on efficient return management to maintain customer satisfaction and minimize costs. Sorting robots are an increasingly popular solution for the return sorting process in logistics due to their speed, accuracy, and flexibility.
In conclusion, sorting robots are a valuable tool for the return sorting process in the logistics industry. Their speed, accuracy, and flexibility make them an ideal solution for sorting packages, managing inventory, maintaining quality control, optimizing capacity, and reducing labour costs. As logistics companies continue to seek new ways to improve their return management processes, sorting robots are likely to become an increasingly essential part of their operations.
Challenges in deploying sorting robots in the express logistics supply chain
Despite their many benefits, these systems also have several disadvantages that should be considered before implementation.
Challenge | Description |
---|---|
High-cost | The cost of purchasing, installing and maintaining a sorting robot can be substantial. This can be a barrier to entry for many organizations, especially small and medium-sized businesses. |
Speed | Sorting robots need to work quickly and efficiently to handle large volumes of items. This requires fast processing capabilities and precise movements |
Limited Adaptability | These robots are typically designed to sort specific types of items based on specific criteria. This implies they may be unable to deal with changes in the items being sorted or new sorting criteria. |
Integration | Sorting robots need to be seamlessly integrated with other systems, such as inventory management and production systems to ensure that they work efficiently and effectively. This requires compatibility with different software and hardware systems, as well as effective communication and coordination with human operators and other machines. |
Maintenance | Robots require regular maintenance and repair, which can be time-consuming and costly. Additionally, they need to be constantly updated and upgraded to keep pace with new technologies and advancements. |
Dependence on technology | Sorting robots rely heavily on technology, including sensors, software, and algorithms, to sort items accurately. Any malfunction or failure of this technology can result in errors or downtime for the system. |
Sorting robots can be a valuable tool for organizations looking to streamline their sorting processes, however, the high cost, complexity, limited adaptability, and dependence on technology are all important factors to consider when deciding whether to implement this system.
How sorting robot manufacturers are overcoming the challenges
- Lowering capital cost: Robotics manufacturers are working to make sorting robots more affordable for businesses of all sizes. This includes developing more cost-effective hardware and software solutions and offering flexible financing options. Business models like Robotics-as-a-Service (RaaS) are also helping companies easily implement these solutions by making them available on a subscription basis.
- Increased flexibility: The industry is developing sorting robots that are more flexible and adaptable to a wider range of products i.e., developing sorting robots with advanced sensing and perception capabilities that can detect and sort a wider variety of items with greater accuracy.
- Integration with existing systems: Newer iterations of sorting robots come with an improved range of system integration with existing warehouse management systems, order management systems, and other automation technologies. This is done by developing more user-friendly interfaces and software that makes it easier to integrate these units with other systems.
- Maintenance and repair: Robotics companies are currently working on developing solutions for predictive maintenance, which utilize data analytics and machine learning algorithms to forecast when maintenance and repairs will be required. This technology has the potential to minimize downtime and prolong the lifespan of sorting robots.
Future of sorting robots
With a growing demand for automation and increased efficiency across various industries, the future of sorting robots appears promising. Manufacturers of robotics solutions are cognizant of this demand and are continuously upgrading and enhancing their tech. Let’s explore some of the latest trends and advancements in this field and their potential impact on the industry.
- Artificial Intelligence: Advanced artificial intelligence algorithms are being incorporated into modern sorting robots, enabling them to sort objects with greater accuracy and efficiency.
- Integration with other technologies: Sorting robots are anticipated to integrate with other technologies like the Internet of Things (IoT) and Big Data, thereby improving efficiency and accuracy in the sorting process.
- Greater customization: In the future, robotic sortation is likely to become even more customizable, allowing businesses to tailor the sorting process to their specific needs.
- Improved sensors: These robots are expected to feature more advanced sensors, resulting in greater precision and accuracy in the sorting process.
- Expanded applications: Sorting robots are likely to find new applications in industries such as healthcare and education, which could benefit significantly from automation.
- Cost reduction: Manufacturers are striving to reduce the cost of sorting robots through design innovations and economies of scale to make them more accessible to businesses of all sizes.
Choosing Unbox Robotics for your sorting needs
Unbox Robotics has developed “Unboxsort” a first-of-its-kind vertical parcel sorting and order consolidation solution, which addresses various key concerns plaguing the warehouse automation industry like productivity, space utilization, flexibility and capital.
What sets Unbox Robotics apart from others? Here are some reasons why you should consider using Unbox Robotics for all your sorting needs.
- Dependable and all-inclusive support: Unbox Robotics offers a complete solution that includes installation, training, 24*7 support and maintenance of the multi-bot system.
- Feature-rich shipment feeding system: The shipment feeding system is equipped with multiple features such as dimensioning, weighing, scanning and rejection systems that are integrated into a single module.
- Increased efficiency: The UnboxSort system has a sorting accuracy rate of 99.99% and improves personnel productivity by 3 times.
- Space Efficient Systems: The modularity of the UnboxSort solutions helps in providing a solution which saves up to 50-70% of the warehouse footprint.
- Scalability of the robots: Unbox Robotics provides a highly scalable system capable of handling throughput capacities ranging from 500 to 20,000 packages per hour and accommodating over 100 destinations for sorting.
- Assured Adaptability: Depending on business requirements, you can scale up or down using a pay-per-use model (Robotics-as-a-Service). This model allows enterprises to automate as OPEX and makes automation within reach for more businesses.
- Quick Launch: It takes less than two weeks to implement the UnboxSort system.
The Technology behind Unbox Robotics patented technology “UnboxSort”.
The Unbox Robotics solution features a patented system that deploys a fleet of mobile 3D sorting robots, called the UnboxSort. The solution is designed to sort packages vertically, thus improving space efficiency and also making it ideal for use in small to mid-sized logistics operations.
The system includes the following components: the robot unit (UnboxSort), a Multi-Robot System guided by a proprietary ACO (Ant Colony Optimization) algorithm, a Dynamic Binning module, Smart Racks, and space efficient process layout.
Sorting robotics for automated organizing and sorting
Sorting robots are revolutionizing the way things are done and have the potential to bring about significant changes in various industries. They are enhancing sorting accuracy while decreasing human labour demands and increasing efficiency. While considering warehouse sortation for your company, it is crucial to do a thorough analysis of different operations and processes that can and cannot be automated.
Unbox Robotics, a reputable supplier of warehouse automation robotics solutions, can help you automate your express logistics supply chain operations and has the knowledge and expertise to work with you to evaluate your processes and provide the best automation recommendations and solutions. The scalability, fast deployment, and adaptability of the Robotics-as-a-Service model provided by Unbox Robotics help retailers of any size implement automation into their processes easily.